IMPORTANT: The following is a basic list of things that every user of wire rope should be aware of to safely use wire rope winch lines and slings. It is intended to provide basic information and is not a complete discussion. Links to sources of more information are provided starting on page 97 of our catalog.
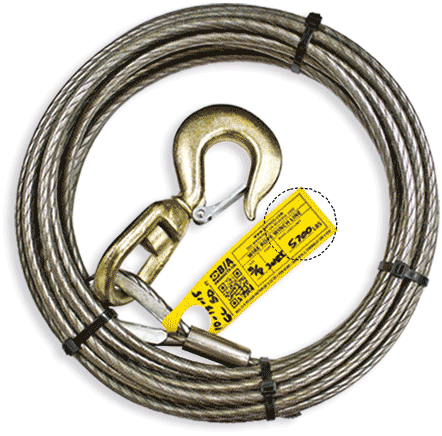
Never exceed the work load limit of a wire rope
THE WORK LOAD LIMIT IS BASED ON THE NOMINAL STRENGTH OF A NEW, UNUSED WIRE ROPE
DETERMINE THE WORK LOAD LIMIT OF A WIRE ROPE: The nominal strength divided by a design factor determines the Work Load Limit of a Wire Rope. The design factor will vary depending on the intepart nded use of the wire rope and machine or equipment it is installed on. Design Factors have been established by OSHA, ANSI, ASME, SAE and other governmental and industrial organizations.
No wire rope should ever be installed or used without full knowledge and consideration of the Work Load Limit. You must determine if the Work Load Limit is suitable for your use.
NOMINAL STRENGTH
÷ DIVIDED BY
DESIGN FACTOR
= EQUALS
WORK LOAD LIMIT
Wire rope wears out
THE STRENGTH OF A WIRE ROPE DECREASES WITH EACH USE
WIRE ROPE WILL FAIL IF IT IS:
WORN OUT / OVERLOADED / MISUSED / DAMAGED / IMPROPERLY MAINTAINED
NEVER OVERLOAD A WIRE ROPE.
Any load greater than the Work Load Limit is an overload (it is so important we said it twice). Never shock load a wire rope.
Most wire rope installations require periodic inspection and record keeping of inspections by a qualified person. The purpose of the inspections is to determine if the wire rope is suitable for safe use in its intended purpose. Inspection criteria and removal from service criteria have been established by OSHA, ANSI, ASME and similar organizations. In addition, the inspection should include the condition of the sheaves, drums and any other equipment the wire rope comes in contact with. See page 111 of our catalog for more sources of information.
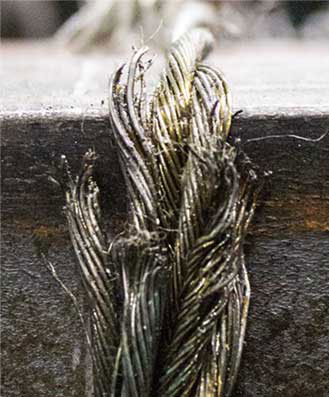
Parts of the wire rope
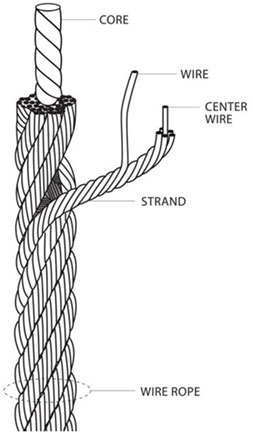
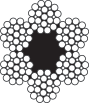
6X25 EIPS | Extra Improved Plow Steel |
FC | Fiber Core |
6 strands | 19-25 individual wires per strand |
Finish | Bright (Plain Steel) with light oil |
Flexibility | lube |
▧▧▧▧▧ |
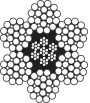
6X25 EIPS | Extra Improved Plow Steel |
IWRC | Independent Wire Rope Center |
6 strands | 19-25 individual wires per strand |
Finish | Bright (Plain Steel) with light oil |
Flexibility | lube |
▧▧▧▧ |
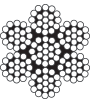
7X19 GAC | Extra Improved Plow Steel |
IWRC | Independent Wire Rope Center |
7 strands | 19 individual wires per strand |
Finish | Galvanized for corrosion |
Flexibility | protection |
▧▧▧ |
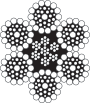
6X37 EIPS | Extra Improved Plow Steel |
IWRC | Independent Wire Rope Center |
6 strands | 6 strands of 37 individual wires |
Finish | Bright (Plain Steel) with light oil |
Flexibility | lube |
▧▧▧▧▧▧ |
HOW TO MEASURE WIRE ROPE DIAMETER
WIRE ROPE DIAMETER IS MEASURED AT THE OUTERMOST DIAMETER OF THE STRANDS.
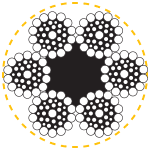
DESIRED MEASUREMENT
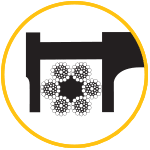
CORRECT WAY TO MEASURE WITH CALIPERS
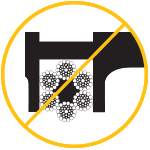
INCORRECT WAY TO MEASURE WITH CALIPERS
OPERATING PRACTICES
SHEAVES & DRUMS
When an inspector examines a rope, he may see sections showing excessive wear. By flagging the rope, he can quickly determine where the rope is rubbing or contacting parts of the equipment, and then repair, replace, or modify the condition causing the wear. Inspection of sheaves is a relatively simple, yet vital task.
Sheaves should be checked for:
- Correct groove diameter.
- Roundness or contour to give proper support to the rope.
- Small holes, cracks, uneven surfaces, or other defects which might be detrimental to the rope.
- Extreme deep wear.
A sheave should also be checked to make sure it turns freely, is properly aligned, has no broken or cracked flanges, and has bearings that work properly.
Drums should also be inspected for signs of wear which could damage rope. Operating with a smooth drum calls for special care. Be sure the rope is always tightly wound and thread laid on the first layer. Any loosening of the line is easily observed as the winding will be bad and the rope will be coming off with a series of “bad spots.” Other places of contact such as rollers, scrub boards, guides and end attachments should also be inspected.
UNWINDING WIRE ROPE
A wire rope can be damaged permanently even before it has gone into operation. Short lengths of wire rope often come in coils. Uncoil these lengths by rolling the coil slowly like a wheel, leaving behind a trail of straight rope. (Uncoiling by laying the coil flat and pulling off the top can create kinks and make the rope hard to handle.)
When spooling onto operating drums, best service will be received if the rope can be first laid out straight on the ground prior to reeling and then pulled into the system under tension.
FREQUENT INSPECTION
Wire rope shall be visually inspected by the person handling wire rope each day it is used. These visual observations should be concerned with discovering gross damage, such as listed below, which may be an immediate hazard:
- Distortion of rope such as kinking, crushing, unstranding, birdcaging, main strand displacement, or core protrusion. Loss of rope diameter in short rope lengths or unevenness of outer strands should provide evidence the rope should be replaced.
- General corrosion.
- Broken or cut strands.
- Number, distribution, and type of visible broken wires.
PERIODIC INSPECTION
A periodic inspection shall be performed by a designated person on a regular basis with frequency of inspection based on:
- Frequency of wire rope use.
- Severity of service conditions.
- Nature of lifts being made.
- Experience gained on the service life of wire rope used in similar circumstances.
REMOVAL FROM SERVICE
Wire rope shall be immediately removed from service if any of the following conditions are present:
- Kinks, bird caging or popped core in the working section of the wire rope.
- Discoloration due to excessive heat.
- Corrosion with pitting of the wires.
- More than 11 broken wires in 6 diameters of length.
- More than 3 broken wires in any one strand.
- More than 2 broken wires at the end connection.
FOR MORE INFORMATION, PLEASE VISIT
The Wire Rope Technical Board online: www.wireropetechnicalboard.org
AWRF (Associated Wire Rope Fabricators): www.awrf.org
OSHA: www.osha.gov
ASME: www.asme.org